Fluoropolymer coatings offer valuable benefits for thousands of industrial applications, but these coatings are only as good as they last.
Unfortunately, durability is not inherent to Fluoropolymer coatings. That’s why Whitford developed Excalibur. Fluoropolymer coatings are organic and, by definition, are soft. They are coated over a substrate with no more than surface cleaning and, frequently, abrading. So the coating remains separate from the substrate, simply layered over the surface.
Excalibur on Cable Connector Molds
As a result, conventional coatings wear quickly, losing the low friction, release and corrosion resistance so important to applications such as industrial bakeware, copy rollers, molds, etc.
But Excalibur is not just a Fluoropolymer coating, it is a unique reinforced system. What makes it different from – and superior to – all conventional Fluoropolymer coatings is its remarkably superior resistance to wear and to all forms of abrasion.
A patented stainless-steel alloy is the secret of Excalibur’s superior resistance to wear. Excalibur actually becomes part of the surface to which it is applied, offering the strength of stainless steel with the low friction, release and corrosion resistance of the finest fluoropolymers.
Under abrasive treatment, rough elements simply skip along the stainless-steel “peaks”, unable to gouge out the Fluoropolymer coatings protected in the “valleys”. (See “The Excalibur Process.”) So Excalibur retains its durability, corrosion resistance, low friction and release qualities, even under the harshest conditions.
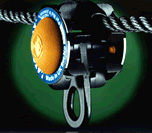

Learn More About Excalibur® Fluoropolymer Coatings Here:
Excalibur Fluoropolymer Coatings Why Excalibur Fluoropolymer Coatings? The Excalibur Process Excalibur Test Results When to Use Excalibur