Category Archive: Sun Coatings
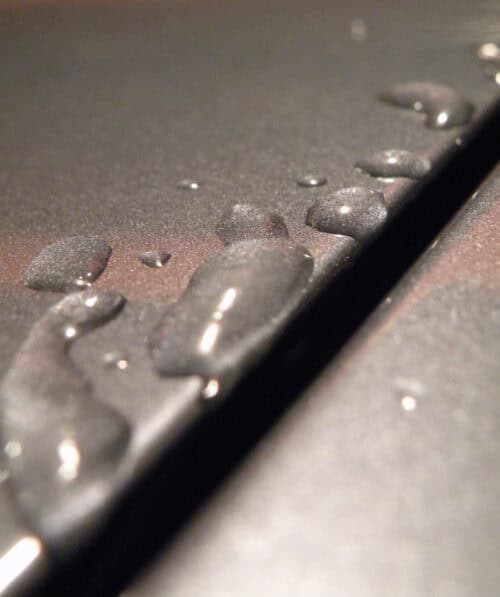
Superhydrophobic coatings are high-performance surface coatings that have the ability to cause water and other liquids to resist wetting a surface. Superhydrophobic coatings form a microscopic, roughened surface texture that traps air in the microscopic grooves of the surface that causes the water to bead up and roll off instead of spreading. They are widely used across various industries for protecting equipment from moisture, corrosion, and the elements.
How Superhydrophobic Coatings Work
The key to superhydrophobic coatings is their unique molecular architecture that replicates the natural surfaces found in lotus leaves. The coatings disrupt surface tension, and almost nothing adheres to them, including water or pollutants. What one gets is enhanced durability, enhanced performance, and low maintenance.
Industries Benefiting from Superhydrophobic Coatings
Superhydrophobic coatings are worth their weight in gold in the majority of industries because they can repel water and prevent moisture-caused damage. In the aerospace industry, they protect aircraft components from ice, rain, and humidity, thus increasing durability. In the automobile industry, they protect cars against water spots, corrosion, and prolong car life. In the healthcare industry, they protect equipment from becoming dirty and contaminated with bacteria, improving hygiene and safety. They depend on these coatings to shield equipment and tools from damage by water, thus extending the life of the latter. Moreover, when used in the food industry, they keep liquids and contaminants from coming into contact with equipment so that equipment remains clean and functional.
Benefits of Superhydrophobic Coatings for Equipment Performance
1. Enhanced Durability
By preventing wetting, superhydrophobic coatings extend the lifespan of industrial machinery and equipment. Exposure to water causes rust, corrosion, and material degradation, which are all avoided or reduced by these coatings.
2. Improved Efficiency
In applications like manufacturing and food processing, reducing liquid adhesion minimizes downtime for cleaning and maintenance. This improves overall productivity and reduces operational costs.
3. Corrosion and Contamination Prevention
Industries dealing with harsh chemicals or environmental exposure benefit from superhydrophobic coatings, as they create a protective barrier against corrosion and contamination. This is particularly useful in applications that require adhesive coatings to maintain strong bonding properties.
4. Reduced Maintenance Costs
Since these coatings avoid the settlement of liquids, grime, and dirt, they reduce the number of periodic maintenance and cleanings. Less maintenance is performed on superhydrophobic-treated equipment, with it being operated for longer times.
Sun Coating’s Expertise in Protective Coatings
Sun Coating provides various industrial coatings, including superhydrophobic, that enhance the performance of your equipment in any sector. Through our vast experience with protective solutions, our coatings ensure maximum long-term durability and efficiency for your equipment. Additionally, our Excalibur Fluoropolymer Coatings offer unmatched protection against extreme conditions, making them ideal for applications requiring superior performance and resistance.
Conclusion
Superhydrophobic coatings bring significant benefits to industrial hardware in the shape of enhanced longevity, corrosion prevention, and minimal maintenance. In aerospace, manufacturing, food processing, and all other industries, these coatings provide improved efficiency and extended equipment life. Sun Coating’s experience with advanced coatings ensures your business the best possible protection and performance.
Interested in learning more about how superhydrophobic coatings can benefit your operations? Contact Sun Coating today to explore the best coating solutions for your industry.
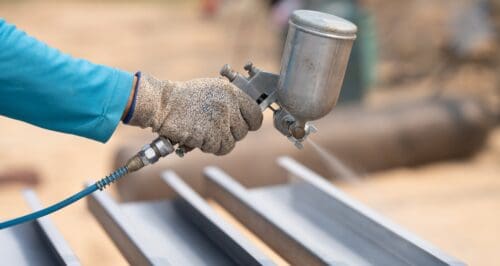
All manufacturing processes are going to rely on metal equipment for production. However, this presents a problem. Metal is vulnerable to a wide array of external threats, both in regard to the manufacturing facilities, if the metal in question is used in the equipment needed for production, as well as in regard to the equipment that metal parts are used for once they leave the facility and are used in business and consumer products. This is where protective coatings come in. Protective coatings are a must for any business involved in industrial production. But how do these protective coatings work? What do you need to consider when seeking protective industrial coatings for your own business purposes? Here’s a closer look at how coatings improve chemical resistance in harsh environments. Once you’re ready to find protective industrial coatings for your business, you can request a quote here from Sun Coating Company.
What Are Industrial Coatings?
Industrial coatings refer to any coating that is applied to a substrate. While there is a myriad of industrial coatings to choose from, such as anti stick coating and powder coatings, the end goal is the same: to apply a protective coating that effectively binds to the underlying substrate so as to protect it against the various stressors and hazards that it will encounter during use. What’s important to note about industrial coatings is that not all coatings are going to be suitable for all environments. Some coatings may be excellent for reducing abrasion but may not be able to hold up so well against chemicals they come in contact with. Others may be chemical resistant but may not hold up against higher temperatures, which can present problems during the manufacturing process and beyond. This presents an important question: which industrial coatings offer chemical resistance, and how?
Examples of Industrial Coatings and How They Improve Chemical Resistance
Not all coatings are chemically resistant, and this is due to the makeup of the product being used. For example, a basic acrylic coating may serve to protect a substrate from abrasion, but chemicals will eat right through it as it’s not able to defend itself against the harsher compounds it comes in contact with. Certain industrial coatings are far more effective at being chemically resistant. How? The industrial coatings that will defy chemicals feature tight molecular bonds and non-porous surfaces that prevent chemicals from working their way into and through the coating. The denser and stronger the coating, the more likely it is to protect substrates against chemicals.
But which protective coatings are chemically resistant? Some of the top coatings worth considering if you’re seeking to defend substrates from chemicals include:
- Fluoropolymer-based coatings, such as Whitford nonstick solutions, are capable of shielding substrates against hydrochloric, nitric, phosphoric, and sulfuric acid, just to name a few. As with many other coatings, you can also expect abrasion resistance and high-temperature resistance.
- Polyurethane-based coatings are adept at defending substrates against a wide range of caustic chemicals as well as other hazards like hydraulic oil, acids, and solvents.
- Epoxy-based coatings are a popular protective coating option. It protects against an array of chemicals, including everything from fatty acids to salt solutions and chemical cleaning detergents.
When you’re looking for chemically resistant industrial protective coatings, you should also consider custom options. Custom industrial coatings will help you get the specific chemical resistance you demand and specific benefits you may not get with broadly tailored products.
Contact Sun Coating Company to Protect Your Equipment and Product
Sun Coating Company is your partner in protecting industrial equipment from caustic chemicals that could cause major damage to exposed substrates. Get in touch with us today to get your quote, or ask us about our various products and services.
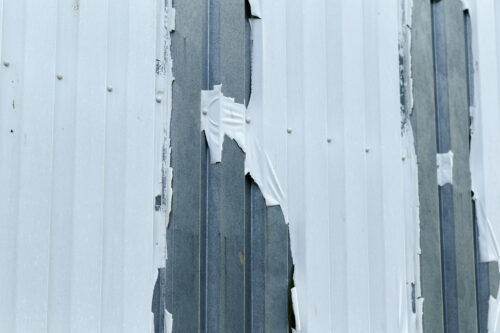
As a leading industrial coatings company, our team at Sun Coating Company understands how frustrating it can be when coatings fail prematurely. Our goal is always to provide coatings that stand the test of time in even the harshest industrial environments. However, despite any company’s best efforts, coatings can still fail sometimes. Here are some of the most common reasons coatings fail and provide tips to help prevent failures.
Surface Preparation Issues
One of the most common reasons industrial coatings fail is inadequate surface preparation. Coatings require a clean, contaminant-free surface to properly adhere. Any dirt, oil, grease, rust, or other contaminants can cause coatings to lose adhesion. Even unseen contaminants like vapor residues can lead to coating failure down the road.
Thoroughly clean and degrease surfaces before coating application. On metals, remove any rust and create the proper surface profile for mechanical bonding. Inadequate surface prep accounts for over 60% of industrial coating failures. Don’t cut corners here.
Incompatible Materials
Coatings are formulated for specific materials like steel, aluminum, and plastic. When a coating isn’t compatible with the substrate, the result is usually premature failure. Using a coating meant for steel on aluminum will likely lead to delamination or blistering.
Always verify coating compatibility and use coatings formulated for your specific substrate. At Sun Coating Company, we can recommend compatible coatings for virtually any substrate. Our coatings, like polyurethane foam mold coatings, are engineered for common industrial materials.
Incorrect Film Thickness
Applying coatings at the wrong film thickness is a very common mistake. Coatings applied too thin won’t provide adequate protection and durability. Overly thick coatings will experience sagging, cracking, or imprinting.
Follow the product data sheet for proper film thickness and confirm thickness with wet film gauges during application. Too thick or thin by more than 10% often leads to failure. Proper film thickness ensures optimal performance.
Curing Issues
Coatings require time and the proper conditions to fully cure. When coatings don’t fully cure, performance will be severely impacted. Coatings may never reach full hardness or chemical resistance.
Allow adequate time for coatings to cure based on product data sheets. Ensure the required temperature and humidity levels for curing are met. Forced curing can be used to accelerate cure times when necessary. Uncured or partially cured coatings will almost always lead to premature failure.
Exposure Before Curing
Exposing coatings to chemicals, abrasion, or other factors before fully curing is another common mistake. Coatings in the curing process are vulnerable. Any exposure can permanently damage the coating, quickly leading to failure once put into service.
Isolate freshly applied coatings from all chemicals, abrasion, fluids, and other factors until completely cured. Avoid touching, walking o,n or otherwise disturbing curing coatings. Patience during the curing process will pay off.
Off-Ratio Mixing
Two-component coatings require mixing resin and catalyst at the proper ratio. When off-ratio mixing occurs, coatings will not cure correctly. They’ll remain tacky and soft, rapidly failing once put into service.
Carefully follow mix ratios and measure components precisely. Calibrate spray equipment regularly to ensure proper metering. Confirm ratios with periodic scrape tests. Off-ratio coatings must be fully removed and reapplied correctly.
Poor Surface Profile
An adequate surface profile provides the mechanical bonding that coatings require for abrasion and impact resistance. Surfaces that are too smooth prevent mechanical bonding, limiting coating adhesion. This is especially important for a dry film lubricant coating.
Achieve the recommended anchor profile for each coating, typically 2+ mils. Blasting, power tools, and chemical etching all create a proper profile. Slick surfaces like stainless steel may require abrasive blasting. The profile should appear uniform and jagged under inspection.
Do You Need an Industrial Coating? Call Us
When an industrial coating fails prematurely, one or more of these factors are usually the root cause. Following the tips provided will help avoid failures and maximize the coating lifespan. Of course, choosing a reputable coatings company like Sun Coating Company is also key. Our experts can recommend the ideal coating system for your specific application challenges. Reach out to us to get started improving your industrial coating performance. We look forward to partnering with you.
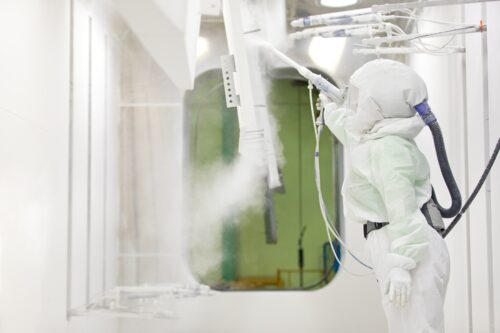
Industrial protective coatings are a must-have for equipment longevity and manufacturing support. But the bulk of the advice that you’ll receive when it comes to coatings is in regard to elements of the coatings themselves, such as the types of coatings, the required application and maintenance, and so on. But one question almost every business will find themselves faced with when shopping around for coatings is, how do I ensure that I’m turning to the right coating supplier for my business? Choosing the wrong coating supplier can leave you with low-quality products and services that create more issues than they solve. If you’re interested in getting it right the first time, consider the helpful insights offered below, and request a quote from Sun Company to get the support and service you deserve!
Consider Which Coatings You’re Interested in
The first thing to look into when you begin looking at coating suppliers is their inventory. Consider which coatings you’re interested in when you start the shopping process. Not all suppliers may carry all types of coatings or offer the needed coating-related services. For example, you may find one supplier that appeals to you, but if you settle on them without doing any further research and discover that they don’t offer the food processing coatings your business needs, you’re going to be right back at square one. Always make a list of the products or services you need, then begin shopping for them.
Conduct Extensive Company Research
Now that you have a list of coatings in mind, it’s time to begin looking at coating suppliers. Finding the right coating suppliers is like finding the right business for any of your needs, personal or business-related. You’ll want to conduct extensive company research, focusing on the following:
- Time in Business: Time in business isn’t necessarily a must when you’re trying to find the right coating supplier. However, a company that has been supplying coatings for a significant period of time is one that is going to be able to provide you with the level of support and guidance that you need when you’re seeking out coatings for your industrial equipment. More than that, there’s the potential for new companies to potentially be scams, especially if they just got started and there are red flags around the website. The longer a business has been around, the more likely it is that they’re a high-quality partner in helping you find the right coatings.
- Website and Third-Party Reviews: Reviews will tell you the things that a business won’t. Looking at the reviews and testimonials on a business’s website will give you an idea of how satisfied past customers were so that you can shop form that supplier with confidence. However, some businesses may also only show positive reviews and testimonials. This is why you need to look at third-party review platforms to see if feedback is equally positive there. If everyone seems to be satisfied and issues are limited, it’s a strong indication they’re a coating supplier you can trust.
- Quality of Inventory: When you’re researching coating suppliers, look at their inventory. Do they carry high-quality products like Whitford Xyland coatings? Or, is their inventory filled with low-quality coatings that won’t give you the durability and protection your equipment needs? Making sure they only offer the former is essential to your experience.
Always Ask Questions
Customer support plays a major role in your shopping experience, especially if you need help learning more about coatings and getting recommendations. Reach out to them with any questions you have so you can get a feel for how they treat their customers and if they’ll offer the support you deserve. If they’re rude and unhelpful, seek a new coating supplier!
Request a Quote Today!
Sun Coating Company is your coating supplier and coating services partner, offering you the high-quality coatings, helpful service, and superior results your business needs. Request a quote from us today!
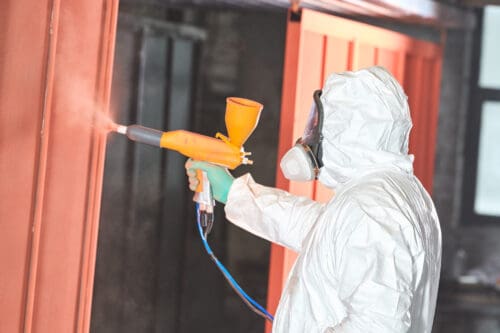
When you’re looking into industrial protective coatings for your business, chances are that you’re only looking for the best. Granted, there are applications for coatings of a perceivedly lesser quality and lower price point if you’re only looking to temporarily coat things. However, most people are going to want the best coating for their needs. But with high-quality coatings come higher-quality costs. One might think, why is this coating significantly less while this coating that offers more worth so much more in comparison? As with any product, there are quite a few reasons. Let’s examine the cost factors of high-performance coatings to get a better idea as to why they cost more than their counterparts. No matter what budget you have or how much you’re willing to spend, Sun Coating Company is always here to help you find the appropriate coatings for your business demands.
Cost Factors Related to High-Performance Coatings
High-performance coatings, in regard to the actual material used to coat your substrates, are going to cost more due to the quality and types of compounds needed to make the coating solution, the complexity of the process required to put everything together (which includes any labor), and the machinery required to manufacture the coating. Whereas cheaper coating solutions may be easier to make overall, high-performance coating solutions will cost you more because they’re more involved, regardless of whether it comes down to sourcing the many additives required to get the best result or the machinery used in the crafting of the coating solution. Keep this in mind, no matter if you’re looking into Cerakote or another brand.
But what about coating services themselves? Why do high-quality coatings cost so much? As the saying goes, you get what you pay for. Companies offering high-quality coating services will charge for the cost of the product itself as well as the time and labor that goes into making sure your parts are properly coated. Put simply, the level of effort and the amount of work/materials that goes into coating solutions and coatings themselves will determine the price point that is set for these products and services. If you want great work for a large part using a custom solution, you may expect to pay more. If you have something small that requires a coating that isn’t overly involved, you can expect to pay less.
Should Cost Be a Factor When You’re in Need of Coatings?
Cost and affordability are naturally going to be a factor when you’re seeking out solutions for your business. But don’t think that you need to spring for the cheapest thing that you can find. Whether you’re looking into coating solutions to coating services, ask yourself, can I afford to deal with a mistake should these coatings not work out as intended? Getting a coating right the first time is often much better than getting the cheapest option and discovering you need to do it all over again, which can be even more costly should the part be on its way to a customer whose business you might lose or attached to equipment in your factory that is immediately exposed to external elements that will begin eroding the substrate beneath it. Always consider the pros and cons before making any investment, be it an extremely cheap one or a more costly one!
Find Coating Services Designed Around Your Business With Sun Coating Company
Here at Sun Coating Company, we’re dedicated to providing you with high-quality coating services that you can rely on. No matter whether you want Teflon FEP coatings, basic acrylic coatings, or something else, you can trust that the job is getting done as best as possible when you come to us. Contact us now to request a quote for your industrial coatings!
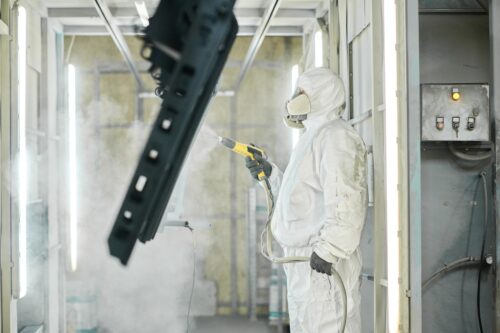
The key to selecting the right industrial protective coating for substrates is having a solid understanding of what it is you’re considering buying, the benefits it offers, and how it varies from similar products you’re interested in. Let’s say, for example, that you’ve found yourself looking at polytetrafluorethylene (PTFE) coating and perfluoroalkoxy (PFA) coating. While similar, there are differences that will determine which you use for industrial purposes. Here’s what you need to know about the differences between PTFE and PFA coatings so you can select the right one for your purposes. Once you’re confident that you’re ready to choose an industrial protective coating, Sun Coating Company is here to help you source the best coatings for your needs!
What Are PTFE and PFA Coatings?
PTFE is a compound that might not sound too familiar until you hear the name Teflon. PTFE is a fluoropolymer that most might associate with cookware, although it is used in manufacturing as well. PTFE is a common coating for parts like gears, slide bearings, and similar parts that grind against each other. It offers a wide range of benefits, like low friction, chemical resistance, and abrasion resistance. So what is PFA? PFA is another fluoropolymer designed by Teflon. It offers many of the same benefits as PTFE, which is to be expected as both are products of Teflon. But that begs the question: If both of these protective coatings are so similar, what is the difference between the two? How do you determine which one you choose, whether you’re looking into automotive Teflon coating companies or other industries?
What Are the Key Differences Between the Two?
PTFE and PFA coatings are largely similar, but there are some minor distinctions that will determine how they’re applied and whether you use them in your operations. Key differences between PTFE and PFA coatings include:
- Thickness: PFA is thicker than PTFE, which is an important consideration when seeking to extend the life and durability of equipment.
- Temperature Resistance: PTFE and PFA are said to have around the same temperature resistance. Some say that PFA is better than PTFE in this regard, while others state that the opposite is true. It’s best to assume that you’re going to have the same degree of heat resistance whether you choose PFA or PTFE to ensure that you receive the desired benefits.
- Hydrophobic Properties: Water and weathering are a much larger concern with PFA coatings than with PTFE coatings. The latter is hydrophobic.
- Flexibility: PFA is more flexible than PTFE, but it’s important to note that it has a much lower flex life by comparison.
- Dielectric Strength: PFA’s dielectric strength is several times stronger than PTFE.
- Chemical Resistance: PFA is said to be more resistant to chemicals than PTFE, although it is vulnerable to certain chemicals such as fluorine atoms and alkali.
- Price: PFA costs a bit more due to its production process, making PTFE the more cost-effective option of the two.
PTFE and PFA coatings offer many of the same advantages and disadvantages, but they have distinct ones as well. Before you select either PTFE or PFA coatings for your industrial needs, take care to carefully research both and understand how these differences can impact their applications in your facilities.
Request Your Quote Now
Sun Coating Company is your source for custom industrial coatings. Whether you’re interested in Sandstrom Coating or many of the other brands and proprietary blends we carry, we can help you find the right industrial protective coating that will offer you the best results, no matter what industry you’re in or the reason for needing protective coating. If you’re ready to support your business operations, get in touch with us to request your quote today!
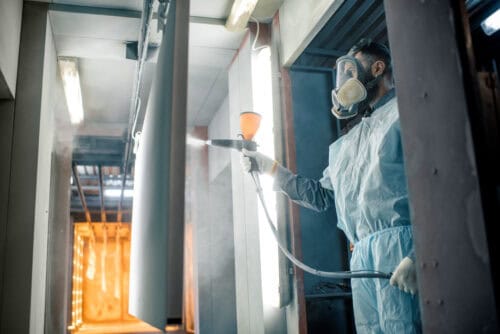
Industrial coatings are an invaluable addition to industrial equipment. With the right coatings, you can reduce the risk of corrosion and other forms of damage affecting industrial machinery, which offers benefits like reduced maintenance and equipment replacement costs, improved productivity, and less downtime. But while industrial coatings offer an additional layer of protection on substrates, they will still wear down over time too. Knowing when you might expect to replace your industrial coatings can help you develop a more comprehensive maintenance schedule so you know when you might need to coat your equipment again to prevent damage to the underlying substrate. But how long do industrial coatings last? The answer will vary, but we’ll break down some average lifespans for industrial coatings, factors that play into the lifespan of coatings, and more to help you make the most of your coatings. If you’re ready to coat your equipment, you can reach out to us here at Sun Coating Company to get the level of support and high-quality services that your business deserves!
How Long Can You Expect Your Industrial Coating to Last?
It’s important to remember that different coatings are naturally going to have different lifespans. Some types of coatings, like ceramic coatings may have a projected lifespan of two to five years. Other coatings like epoxy and polyurethane coatings may last much longer, making it up to 20 years before they start showing signs of wear and need to be replaced. Generally speaking, the broad range of coatings have a lifespan of anywhere from 5 to 20 years, with some being outliers that last a few years less and those that are projected to last as long as 40 years. When you’re looking for industrial coatings, make sure to take a close look at each of the coatings at your disposal to see how long they tend to last. This will give you a better idea as to when you might need to replace it after you receive industrial coating services.
But with the above in mind, not all lifespans are going to be guaranteed. There are numerous factors that will impact lifespan, potentially reducing the lifespan of your coatings.
So, what are these?
What Impacts Lifespan, and How Can You Make Sure Your Coating Lasts Longer?
High-performance industrial coatings that are designed with durability in mind are going to last longer than cheaper, less complex options. However, they may only last as long as anticipated went they encounter the least amount of stress. Factors that can impact a coating’s lifespan include exposure to UV rays, moisture, high chemical exposure, and stress or force. Even those that are designed for these are still going to experience wear and tear. They’re not indestructible. Taking care to purchase industrial coatings that are designed to last but making sure not to test them extensively by exposing them to the harshest of elements constantly will help you see the end of the lifespan spectrum.
That being said, there are things you can do to improve lifespan as well. Whether you’re purchasing heat seal packaging coatings or coatings for the agricultural industry, you can keep your coatings in optimal condition by adhering to best practices during the application process so that the coating doesn’t degrade earlier than it should, regularly inspecting and conducting maintenance on coatings if you notice any concerning signs (cracking, changes in color, etc.), and cleaning your coating often with the right cleaners for the type of coatings you have. The better you care for your coatings and the more you take care to avoid harsh conditions that threaten them, the longer they’ll last.
Get High-Quality Coating Options and Services With Sun Coating Company
Lifespan will vary, but you can make sure your coatings will last longer by choosing the right coating company for superior application and correct coating choice. Start here with Sun Coating Company for your industrial coating needs. Request a quote from us today!
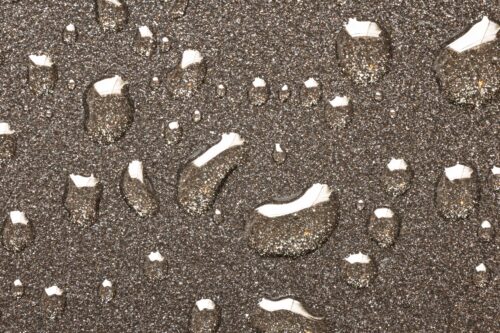
At Sun Coating Company, we frequently receive inquiries about one of our most popular industrial coatings: PTFE, also known as Teflon. PTFE has become a staple across many manufacturing sectors due to its many benefits. Here are 9 key benefits PTFE coatings can provide for your manufacturing operation.
Reduce Friction and Wear
A primary reason behind PTFE’s widespread use is its ability to reduce friction and wear. The coating provides an ultra-smooth surface that enables parts to glide past each other with ease. This reduces friction, which in turn lowers operating temperatures. With less friction, equipment experiences less wear over time, leading to extended service life. PTFE coatings are ideal for applications involving bearings, gears, and other moving components. The reduced friction can also improve efficiency by lowering the energy required to operate equipment.
Prevent Corrosion
In addition to lubrication, PTFE forms a protective barrier that shields metal surfaces from moisture, chemicals, and other corrosive substances. Parts coated with PTFE are far less prone to rusting, pitting, and other corrosion damage. This is especially beneficial for equipment used in harsh industrial environments. PTFE will extend the usable life of components exposed to corrosive agents.
Non-Stick Properties
The non-stick nature of PTFE is invaluable for many manufacturing processes. PTFE-coated parts release adhesives, inks, oils, melted plastics, and other substances much more easily. This prevents fouling and buildup on equipment such as molds, dies, rollers, and more. Frequent cleaning and maintenance are reduced, minimizing downtime. The non-stick properties also improve product quality by preventing defects caused by materials sticking where they shouldn’t.
Temperature Resistance
PTFE excels in high-temperature applications, with upper use limits around 500°F. It maintains integrity and performance well beyond the temperatures that cause other lubricants and coatings to degrade. PTFE’s stability at elevated temperatures allows it to protect components like molds, kiln-car furniture, and other hot equipment. It’s also useful for cooking equipment, heat exchangers, bakeware, and other high-heat applications.
Chemical Resistance
In addition to heat resistance, PTFE stands up extremely well to a wide range of harsh chemicals. Acids, caustics, solvents, and other chemicals won’t deteriorate a PTFE coating. This allows it to protect parts used in chemical processing and other applications where aggressive substances are present. The chemical resistance also enables easy cleaning without damaging the PTFE coating.
Nontoxic and Inert
Unlike some industrial coatings, PTFE is completely non-toxic and chemically inert. This means it won’t react with or contaminate materials it contacts. As a result, PTFE-coated parts are safe for applications involving food, pharmaceuticals, and sensitive electronics where toxicity is a concern. It also makes PTFE suitable for biomedical implants and devices.
Improved Efficiency
By reducing friction and wear, preventing fouling, and minimizing cleaning needs, PTFE coatings allow equipment to operate more efficiently. Less energy and labor are required throughout manufacturing processes, cutting costs and improving productivity. Efficiency gains can be substantial over the lifespan of equipment.
Cost Savings
When you add up all the benefits, PTFE coatings save real money in manufacturing. Longer equipment life, reduced maintenance, minimized downtime, and improved efficiency provide major cost savings over uncoated components. The return on investment from PTFE coating can be quite high in many applications. The coatings pay for themselves over time while improving operations.
Easy Application
Applying PTFE coatings requires no special equipment or complicated processes. Coatings like our Sandstrom Mil Spec offerings can be sprayed, dipped, or brushed on. Curing occurs rapidly at relatively low temperatures for most PTFE coating formulas. We handle the PTFE coating application at our facility, so your parts are ready to install when you receive them.
Ready to Learn More? Call Us!
If your manufacturing process involves equipment that could benefit from lower friction, enhanced wear resistance, non-stick properties, or chemical resistance, PTFE is worth exploring. Please reach out to the team at Sun Coating Company to discuss which PTFE coating best suits your specific application needs. We also offer specialized coatings like Cerakote for extreme high-temperature uses. Contact us today to learn more!

When you think about potential dangers to your industrial machinery, what comes to mind? Most people are worried about damage caused by frequent manufacturing processes, things like chemicals or high temperatures, and similar industrial dangers. But there’s actually something that can be equally as problematic for industrial machinery: winter. The winter season can be quite impactful on equipment, which can be surprising to many organizations who might be running into issues when it’s colder. But why does this happen? Here’s why winter weather increases the need for protective coatings and how Sun Coating Company can help you protect your equipment.
It Introduces Moisture and Harsh Conditions
The winter brings with it severe weather conditions. Some who live in regions where the weather is near-constant year-round may see occasional rain or minor temperature drops, but many others encounter snow and rain (or sleet), blizzards, freezing temperatures, and more. When your equipment encounters this severe weather, it can introduce moisture and other harsh conditions to the substrate, causing corrosion and a host of other issues for the various components in your equipment. Protective coatings prevent moisture from affecting the substrate and keep other harsh winter conditions out as well.
It Causes Machines to Become More Sluggish and Struggle to Work
Have you noticed that your machines have begun to slow down? Some noise and squeak reduction coatings might improve things, but not for the reasons that you think. Winter weather hampers the whole of manufacturing equipment, affecting motors, batteries, and all the individual parts of your machinery. In the case of machinery with lubricants and fluids, winter weather will also slow things down by affecting these aspects of your machinery (in which case, you can not only apply the right coating to your tubing but also look for winter-grade fluids that will hold up against the weather too). During winter, things just run slower, much like we do. But just like we do, adding protective coatings and additional layers helps us to keep the cold at bay, ensuring that we’re able to function relatively normally with fewer issues when the cold weather makes an appearance. If your manufacturing equipment acts just like you do during the winter, now’s the time to apply protective coatings to your equipment.
It Increases Wear and Tear and Thermal Stress
The winter weather wreaks havoc on substrates. Given that most of your substrates will likely be metal or rubber, you’ll find that these materials can begin breaking down and flaking when winter arrives, damaging them and potentially ruining machinery altogether. But brittleness is just one of the major problems substrates face without protective coatings. Another major problem is thermal stress. Extremely cold temperatures can cause substrates like metal to contract, which can damage the metal and other components nearby. Protective coatings are a great way to shield substrates from wear and tear and thermal stress. The only thing to remember is that not every coating is going to be suitable for all the components in your workplace. Some are designed for substrates like metal and will offer additional benefits like reduced friction that you need to keep everything moving smoothly during the winter and throughout the year. But these wouldn’t work for the tubing that you need to keep safe. In that case, you would need a separate coating for these components. As long as you have coatings specifically designed for all of your machinery, you’ll be able to see a massive improvement come next winter.
Request a Quote From Us Now!
Whether you’re shopping for Excalibur coating or industrial custom coating, you can find the custom coating options and services you need right here at Sun Coating Company. Request a quote from us now to get started!
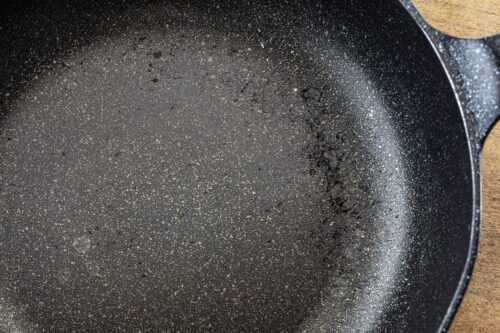
Sourcing coatings for your industrial machinery means having to learn everything you possibly can about your options so you can be confident you’re applying the right coating to each substrate. One popular option that you might be looking into is fluoropolymer coatings. Fluoropolymer coatings are high-performance coatings that are definitely worth considering for your equipment, but there are things that you need to know before you purchase these coatings or coating services. To make sure this is the right coating for your needs, we’ve compiled seven must-know facts about fluoropolymer coatings that you need to be aware of. If you’re sure that fluoropolymer coatings are the correct choice for your industrial equipment, you can enlist the help of us here at Sun Coating Company to help you protect your machinery.
1. Fluoropolymer Coatings Offer Excellent Low Friction Benefits
Fluoropolymer coatings are often used on industrial equipment to reduce friction between certain components that are constantly rubbing against each other throughout various manufacturing processes. This reduces the wear and tear between these elements, increasing lifespan and allowing your machinery to operate optimally. If you want to help your machinery last longer, fluoropolymer coatings’ low friction benefits will be instrumental in making this happen.
2. Extreme Conditions Can Still Cause Damage to These Coatings
Fluoropolymer coatings are a great option because they can hold up against chemicals, heat, and other conditions that are naturally present in an industrial setting. However, it’s important to remember that coatings aren’t necessarily able to hold up to extreme conditions. Pushing your coatings to their limit will cause damage, and fluoropolymer coatings may not be able to hold up to what you need to defend against. They may only be resistant to a degree. Always consider what your substrates are currently encountering and whether your choice of coating will be able to defend against that. This is true no matter whether you’re shopping for Chemours Teflon finishes or something else.
3. There Are Several Types of Industrial Fluoropolymer Coatings
Fluoropolymer coatings come in several forms. You have options like PTFE (Polytetrafluoroethylene), FEP (Fluorinated Ethylene Propylene), and PFA (Perfluoroalkoxy Alkane). Keep this in mind so that you know the terminology when you begin looking into fluoropolymer coatings for your equipment. This brings us to our next point.
4. The Type You Choose Will Impact Your Experience
Different fluoropolymer coatings are going to have different benefits. Some fluoropolymer coatings may stand up well to temperatures of around 500 degrees, but others may start to receive damage below 300 degrees. Some fluoropolymer coatings may be resistant to many chemicals, while others may have weaknesses like alkalis or even water. The type of fluoropolymer coatings you choose will impact how well they function, so take care to do your research and choose the one suited for your environment.
5. Fluoropolymer Coatings Are Applicable Across a Wide Range of Industries
No matter what industry you’re in, you might find an application for fluoropolymer coatings beyond just your equipment. Fluoropolymer coatings are often used in cooking to produce non-stick pans, in the airline industry to protect electric wires and defend against fires, and in the automotive industry to protect vehicles from corrosion and friction.
6. They’re Quite Good at Defending Against Scratches and Abrasion
One might think that fluoropolymer coatings would be a bit weaker than other coatings, but that’s not true. These coatings are adept at keeping scratches and abrasion away from substrates, ensuring that they last longer no matter whether the threat comes from other components or the materials and products being produced.
7. Fading and Discoloration Will Happen in the Sun, But Rapid Degradation Shouldn’t
If your fluoropolymer coatings are exposed to the sun, you may notice fading and discoloration. Fortunately, this isn’t typically a sign of degradation. Fluoropolymer coatings can be applied to equipment that’s used outside, as UV rays won’t cause severe damage, even if they look like they are.
Reach Out to Us Today!
From hot plate welding coatings to motorcycle component coatings, people come to Sun Coating Company for the coating services and high-quality experience their business needs. Get in touch with us today to request a quote for the fluoropolymer coating services that will bolster your business!